As we all know, each hardness test method, whether Brinell, Rockwell, Vickers or portable Leeb hardness tester, has its limitations and is not omnipotent. For large, heavy and irregular geometric workpieces such as the one shown in the following example, many current testing methods use portable Leeb hardness testers to control their hardness.
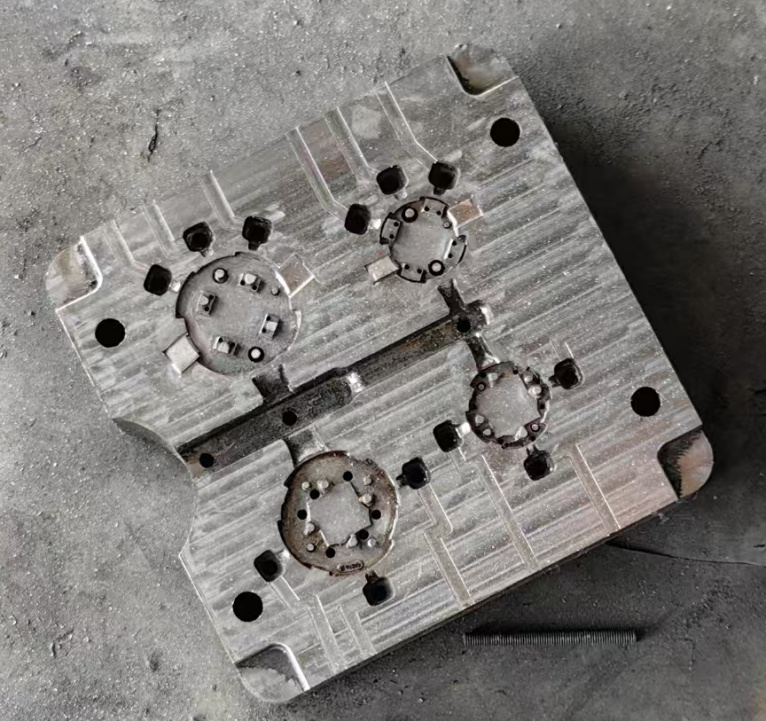
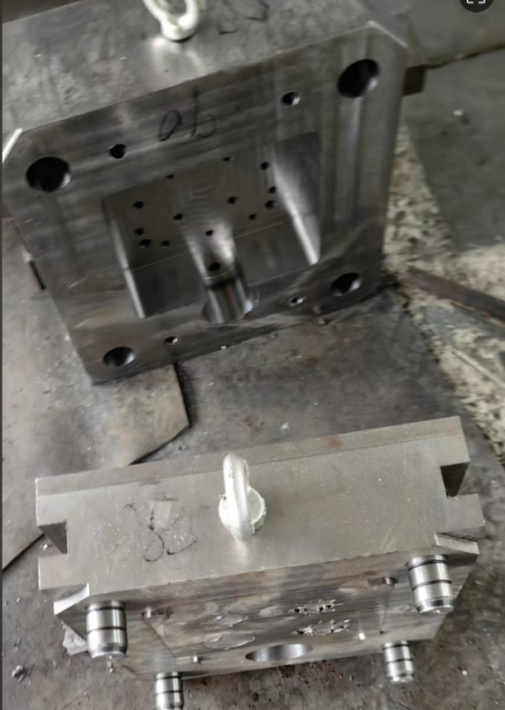
The dynamic measurement method of the Leeb hardness tester has many factors that affect its hardness accuracy: such as: material elastic modulus, ball head consumption, workpiece surface roughness, curvature radius, surface hardened layer depth, etc. Compared with the static measurement methods of Brinell, Rockwell and Vickers, the error is relatively much larger. If the hardness requires higher accuracy, how should we choose a hardness tester?
This kind of heavy workpiece in the process of ordinary hardness tester testing, before the test loading and unloading of the hardness tester, and unloading of the hardness tester will bring a huge workload in the operation process, so how do we choose a hardness tester? The following recommends the use of a hardness tester with a head lifting structure to complete the entire test process. As shown below:
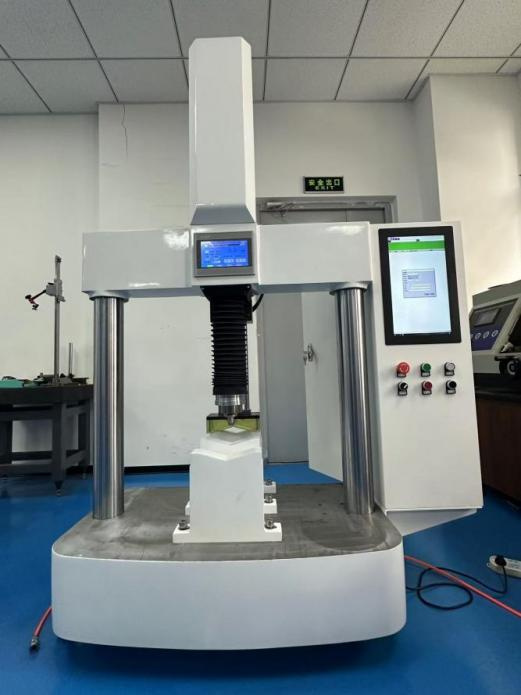
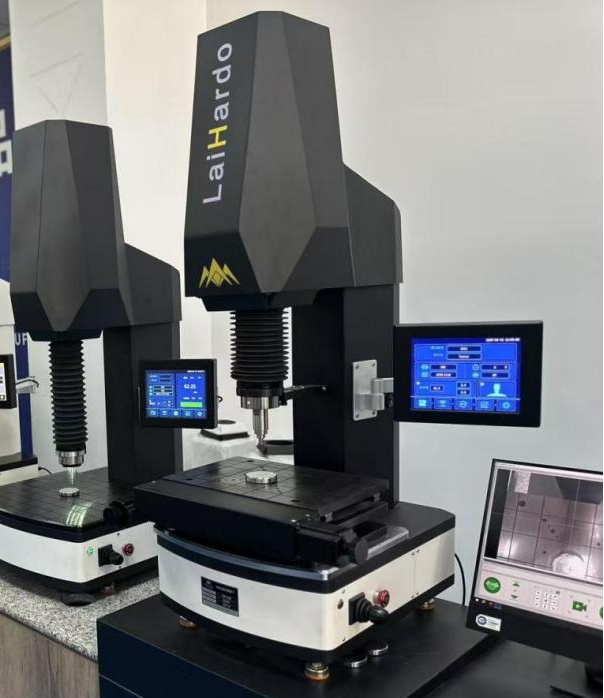
This hardness testing solution can realize Rockwell hardness testing/Vickers and Brinell hardness testing according to hardness testing standards (GB/T 231.1, GB/T 4340.1, ISO6507, ISO6508, ASTM E18, etc.), and meet the high-precision testing and efficient production requirements of heavy workpieces.
The head automatic lifting hardness tester has a fixed workbench, which reduces the error caused by the screw and the lifting of the workbench to the hardness measurement accuracy. The workbench is large in size and can accommodate large weighing workpieces. The one-button measurement greatly reduces the test error and work of the tester, which is convenient and fast.
Post time: Apr-23-2025