How to check if the hardness tester is working normally?
1.The hardness tester should be fully verified once a month.
2. The installation site of the hardness tester should be kept in a dry, vibration-free and non-corrosive place, so as to ensure the accuracy of the instrument during measurement and the stability and reliability of the value during the experiment.
3. When the hardness tester working, it is not allowed to directly touch the surface of the metal to be measured to prevent inaccurate measurement accuracy or damage the diamond cone indenter on the head of the hardness tester.
4. During the use of the diamond indenter, it is necessary to inspect the surface finish of the indenter once a year. After each measurement, the indenter should be put back into the special box for storage.
Hardness tester precautions:
In addition to the special precautions when using various hardness testers, there are some common problems that should be paid attention to, which are listed below:
1. The hardness tester itself will produce two kinds of errors: one is the error caused by the deformation and movement of its parts; the other is the error caused by the hardness parameter exceeding the specified standard. For the second error, the hardness tester needs to be calibrated with a standard block before measurement. For the calibration results of the Rockwell hardness tester, the difference is qualified within ±1. A correction value can be given for a stable value with a difference within ±2. When the difference is outside the range of ±2, it is necessary to calibrate and repair the hardness tester or change to other hardness testing methods.
Each scale of Rockwell hardness has a de facto scope of application, which should be selected correctly according to the regulations. For example, when the hardness is higher than HRB100, the HRC scale should be used for testing; when the hardness is lower than HRC20, the HRB scale should be used for testing. Because the accuracy and sensitivity of the hardness tester are poor when the test range is exceeded, and the hardness value is inaccurate, it is not suitable for use. Other hardness testing methods also have corresponding calibration standards. The standard block used to calibrate the hardness tester cannot be used on both sides, because the hardness of the standard side and the back side are not necessarily the same. It is generally stipulated that the standard block is valid within one year from the calibration date.
2. When replacing the indenter or anvil, pay attention to clean the contact parts. After changing it, test it several times with a steel sample of a certain hardness until the hardness value obtained twice in a row is the same. The purpose is to make the indenter or anvil and the contact part of the testing machine tightly pressed and in good contact, so as not to affect the accuracy of the test results.
3. After the hardness tester is adjusted, when starting to measure the hardness, the first test point is not used. For fear of poor contact between the sample and the anvil, the measured value is inaccurate. After the first point is tested and the hardness tester is in the normal operating mechanism state, the sample is formally tested and the measured hardness value is recorded.
4. If the test piece allows, generally select different parts to test at least three hardness values, take the average value, and take the average value as the hardness value of the test piece.
5. For test pieces with complex shapes, pads of corresponding shapes should be used, and they can be tested after being fixed. The round test piece is generally placed in the V-shaped groove for testing.
6. Before loading, check whether the loading handle is placed in the unloading position. When loading, the action should be light and steady, and do not use too much force. After loading, the loading handle should be placed in the unloading position, so as to prevent the instrument from being under load for a long time, causing plastic deformation and affecting the measurement accuracy.
Vickers, Rockwell hardness
Hardness: It is the ability of a material to resist local plastic deformation, and it is mostly measured by indentation method.
Note: The hardness values cannot be directly compared with each other, and can only be converted through the hardness comparison table.
In 2019, Shandong Shancai Testing Instrument Co., Ltd. joined the National Testing Machine Standardization Technical Committee and participated in the formulation of two national standards
1. GB/T 230.2-2022:"Metallic Materials Rockwell Hardness Test Part 2: Inspection and Calibration of Hardness Testers and Indenters"
2. GB/T 231.2-2022:"Metallic Materials Brinell Hardness Test Part 2: Inspection and Calibration of Hardness Testers"
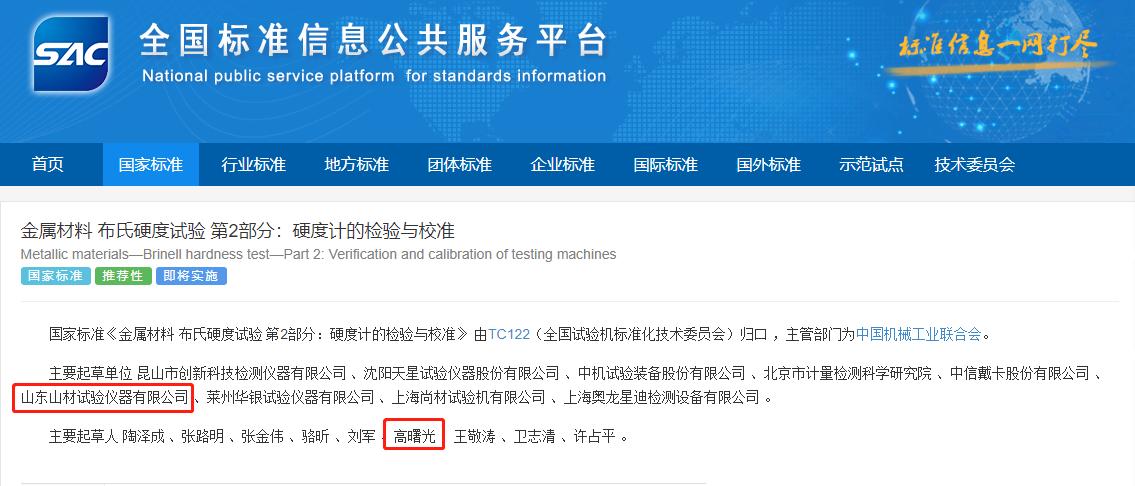
In 2021, Shandong Shancai participated in the construction of the automatic online hardness testing project of aerospace engine pipes, contributing to the aerospace industry of the motherland.
Post time: Dec-29-2022